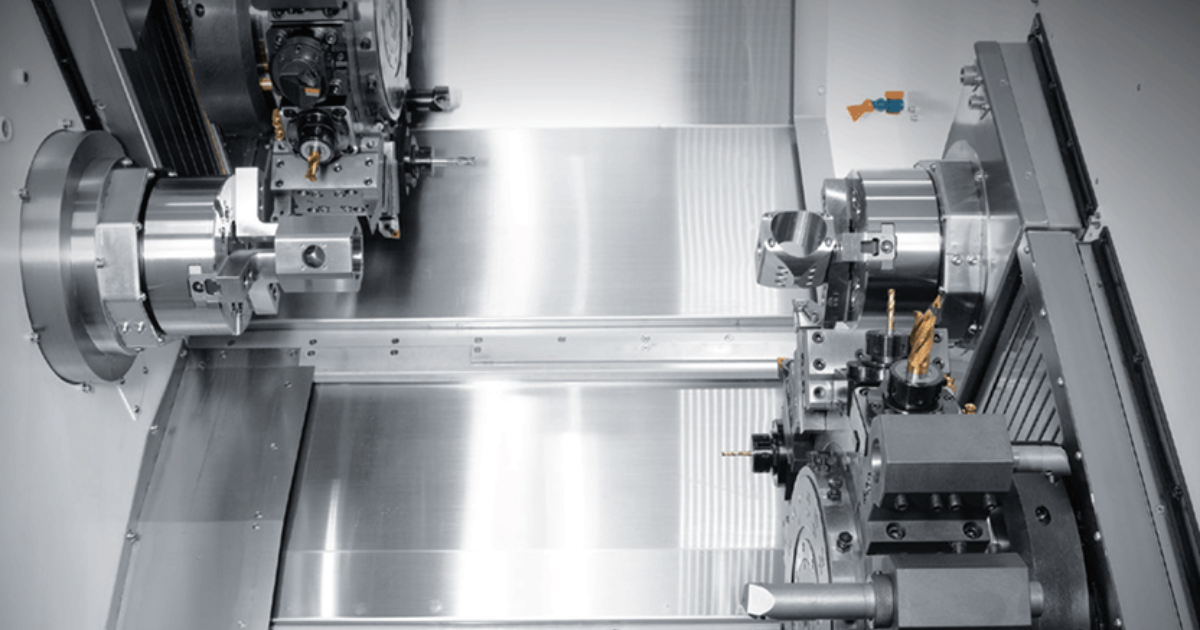
You may also like:
Timeless Tools: The Standard Modern Lathe
Racer Machinery International: Journey Through Generations
Ontario Made Expertise for the Next Generation
Two-spindle CNC machines have revolutionized the manufacturing industry by offering significant advantages in terms of productivity, efficiency, and part quality. By incorporating two spindles, these machines can perform multiple operations simultaneously, reducing cycle times and increasing output.
How Two-Spindle Machines Work
-
- Simultaneous Machining: The primary and secondary spindles can work on different parts simultaneously, maximizing machine utilization.
- Part Transfer: Parts can be automatically transferred between the two spindles, enabling back-working operations and reducing handling time.
- Y-Axis Machining: The Y-axis capability allows for additional machining operations, such as drilling, tapping, and milling.
- Live Tooling: Live tooling enables complex machining operations on both the main and secondary spindles.
Types of Two-Spindle Machines
-
Twin-Spindle Machines:
- Both spindles have identical capabilities and specifications.
- Ideal for high-volume production of identical parts.
-
Dual-Spindle Machines:
- A primary spindle and a secondary spindle with the same chuck size and through-bore capacity but different horsepower.
- Suitable for a wider range of part sizes and complexities.
-
Two-Spindle Machines with Facing Spindles:
- The spindles face each other, allowing for efficient part loading and unloading.
- Well-suited for high-precision and high-volume production.
-
Two-Spindle Machines with Non-Facing Spindles:
- The spindles do not face each other, requiring a manual or gantry-style loading system.
-
More flexible for a variety of part configurations.
Applications of Two-Spindle Machines
Two-spindle CNC machines are highly versatile tools used to produce a wide range of precision components for various industries, including medical and automotive. In the medical field, these machines are employed to manufacture intricate surgical instruments like scalpels, forceps, and clamps, as well as medical implants such as joint replacements and dental implants. Additionally, they are used to produce components for diagnostic equipment like MRI and X-ray machines, and medical devices like pacemakers and defibrillators.
In the automotive industry, twin-spindle CNC machines are used to produce critical engine components such as cylinder heads, blocks, crankshafts, and camshafts, as well as transmission components like gears and shafts. They are also used to manufacture suspension parts like control arms and ball joints, and body parts like doors and hoods.
Benefits
- Increased Productivity: Simultaneous machining and automated part transfer reduce cycle times.
- Improved Part Quality: Fewer handling operations minimize the risk of damage and improve accuracy.
- Reduced Labor Costs: Automated operations reduce the need for manual labor.
- Lower Operating Costs: Efficient use of machine time and reduced energy consumption.
- Enhanced Flexibility: Adaptable to a wide range of part geometries and materials.
By understanding the different types of two-spindle CNC machines and their capabilities, manufacturers can select the optimal machine for their specific production needs, ultimately driving efficiency and profitability.