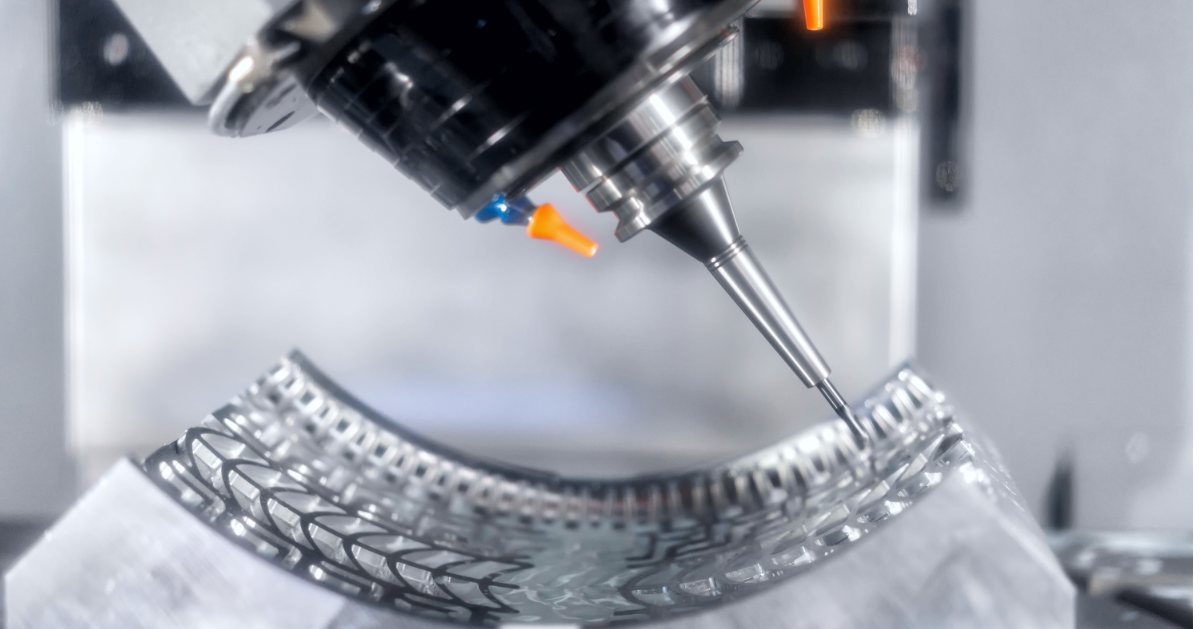
You may also like:
Racer Machinery International: Journey Through Generations
CNC Components: Mechanical Systems
CNC Lathes: What’s on the Horizon?
Computer Numerical Control (CNC) milling machines have revolutionized manufacturing, offering unparalleled precision and efficiency. At the core of these machines lies their ability to move in multiple axes, each contributing to the complexity and accuracy of the final product. Let’s delve into the capabilities of CNC milling machines, from the foundational 3-axis to the cutting-edge 12-axis models.
Understanding CNC Machine Axes
Before diving into the specific capabilities, it’s crucial to understand the axes. A typical CNC milling machine operates on three primary axes:
X-axis: Horizontal movement, left to right.
Y-axis: Horizontal movement, front to back.
Z-axis: Vertical movement, up and down.
Additional axes, often denoted by letters, introduce rotational movement:
A-axis: Rotational movement around the X-axis.
B-axis: Rotational movement around the Y-axis.
C-axis: Rotational movement around the Z-axis.
Beyond these, some machines may have additional axes like U, V, and W, offering even greater flexibility.
3-Axis CNC Milling
The most basic CNC machine, the 3-axis model, excels at creating flat surfaces, drilling holes, and simple 2D shapes. It’s the workhorse of many industries due to its simplicity, affordability, and ease of operation. However, its limitations become apparent when dealing with complex geometries.
4-Axis CNC Milling
By introducing the A-axis, the 4-axis machine gains the ability to create curved surfaces and undercuts. While this expands its capabilities, it’s still restricted in terms of complex shapes due to the limited rotational movement.
5-Axis CNC Milling
The 5-axis machine, with its A and C axes, is a significant leap forward. It allows for simultaneous movement in five directions, enabling the creation of intricate, freeform surfaces. This versatility has made it a staple in industries like aerospace, automotive, and medical device manufacturing.
Beyond the Basics: 7-, 9-, and 12-Axis CNC Milling
As the number of axes increases, so does the machine’s ability to handle complex parts. 7-axis machines, with the addition of a B-axis or E-axis, offer greater flexibility in machining long, slender components. 9-axis machines combine turning and milling operations, increasing efficiency and reducing setup time.
The pinnacle of CNC technology is the 12-axis machine, featuring two cutting heads with independent movement along six axes. This configuration doubles productivity and accuracy, making it ideal for highly complex parts with demanding tolerances.
Choosing the Right CNC Machine
Selecting the appropriate CNC machine depends on the specific requirements of the project. Consider the following factors:
Part complexity: The more complex the part, the more axes you’ll likely need.
Production volume: High-volume production may justify the investment in a multi-axis machine.
Material: Different materials require varying levels of cutting force and precision.
Tolerances: Tight tolerances necessitate a machine with high accuracy and repeatability.
Cost: CNC machines range in price from relatively affordable to extremely expensive.
By carefully evaluating these factors, you can select the optimal CNC machine for your manufacturing needs.
The evolution of CNC milling machines from 3-axis to 12-axis represents a remarkable advancement in manufacturing capabilities. Each additional axis expands the machine’s potential, allowing for the creation of increasingly complex and precise components. As technology continues to progress, we can expect even more sophisticated CNC machines to emerge, pushing the boundaries of what’s possible.