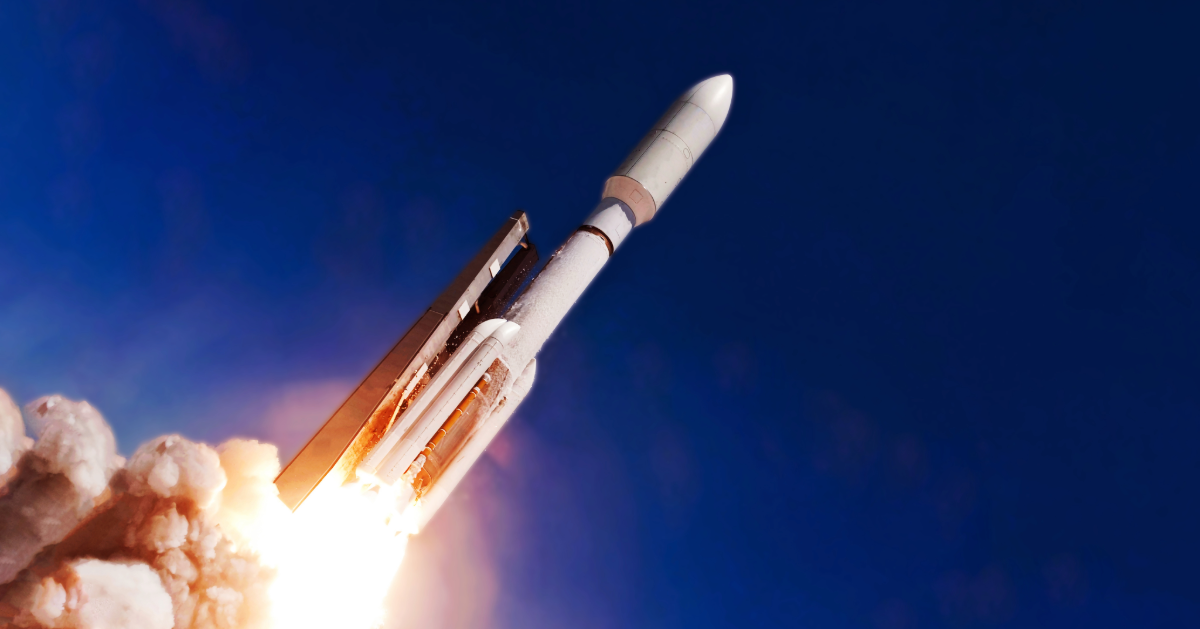
You may also like:
How Digital Twins are Saving Supply Chains
Multitasking Machining: The Future of Manufacturing
Speeds and Feeds: Troubleshooting Guide
The aerospace industry is built on precision and safety, making it essential that every component meets exacting standards. Whether for jet engines, structural supports, or landing gear, aerospace manufacture requires advanced techniques, and CNC (Computer Numerical Control) machining has become a cornerstone of this high-precision production process. In this article, we explore the critical aspects of CNC machining in aerospace manufacturing, including the types of parts produced, materials used, challenges faced, and future trends shaping the industry.
Why Precision is Critical in Aerospace CNC Machining
In aerospace, every part serves a specific function that must align with the highest standards of quality. Aircraft components such as engine parts, structural supports, and landing gear must meet stringent tolerances and geometric precision. A slight deviation in dimensions can have catastrophic consequences.
The primary goal in aerospace CNC machining is to achieve tight tolerances to ensure the safe and efficient operation of parts. For example, aircraft engine components need to fit together perfectly to maintain performance and fuel efficiency. Precision machining not only ensures optimal fit but also reduces friction, wear, and the potential for mechanical failure, contributing to overall aircraft safety.
Additionally, parts that are interchangeably produced in CNC machining help minimize downtime for maintenance and prevent costly delays, such as aircraft-on-ground (AOG) situations, where parts are unavailable for repair.
Types of Aerospace Components Produced via CNC Machining
CNC machining is integral in producing a wide variety of aerospace components. These include:
-
-
- Structural Components: These include elements such as ribs, spars, and flaps, all of which play vital roles in the airframe’s strength and rigidity under stress. Landing gear struts are also precisely machined to handle extreme forces.
- Tail Section Components: This involves machining parts for the vertical and horizontal stabilizers, as well as control surfaces like rudders and elevators.
- Engine and Powertrain Components: From turbine blades to engine mounts, CNC machining handles complex geometries and materials like titanium alloys to produce critical engine parts that must withstand high stresses and temperatures.
- Interior Components: Smaller, yet essential, components like seat tracks, support brackets, and clamps are made with CNC precision to ensure they fit correctly and contribute to the overall safety and comfort of passengers.
- Doors and Hatches: Components such as landing gear doors, passenger doors, and access panels need precise machining for proper fit and sealing, ensuring that these parts perform well under the high-pressure conditions of flight.
-
CNC Machining Processes in Aerospace Manufacturing
Several CNC machining processes are used in aerospace manufacturing, each suited for different types of parts and production volumes.
- 3-Axis CNC Machining: Typically used for simpler geometries, 3-axis CNC machining is effective for parts like fuel pumps and motor housings. It’s particularly beneficial for larger parts where material removal efficiency is crucial.
- 5-Axis CNC Machining: For parts with complex geometries, like turbine blades or impellers, 5-axis CNC machining is ideal. The ability to approach a part from multiple angles allows for better surface finishes, reduced setup times, and more efficient material removal.
- CNC Turning: Used for cylindrical or round parts, CNC turning is essential for producing components such as fasteners, bushings, and shafts. The rotation of the stock combined with material removal ensures precise results.
- CNC Grinding: For components requiring a smooth finish and high tolerance, such as shafts and bearings, CNC grinding is employed to refine surfaces without affecting part dimensions.
Additive Manufacturing Integration: CNC machining and additive manufacturing (3D printing) can be integrated, allowing for hybrid production that combines the design flexibility of 3D printing with the precision of CNC machining
Material Considerations for Aerospace CNC Machining
Aerospace CNC machining demands materials that are strong, lightweight, and capable of withstanding extreme conditions. Key materials include:
- Aluminum Alloys: Aluminum is widely used for its light weight, strength, and corrosion resistance. Common alloys such as 2024, 6061, and 7075 are employed for structural and engine components.
- Titanium Alloys: Known for their high strength-to-weight ratio and resistance to high temperatures, titanium alloys are ideal for parts like engine casings, landing gear, and airframes.
- Superalloys: Materials like Inconel, used for turbine blades and engine parts, offer excellent performance in extreme heat and pressure conditions.
- Composite Materials: Carbon fiber and fiberglass composites are lightweight and offer high strength, making them perfect for parts like wings and fuselage panels in modern aircraft.
- High-Performance Polymers: Polymers such as PEEK and ULTEM are used for non-metallic aerospace components, like electrical cable insulation and some engine parts.
The Role of CNC Machining in Aerospace Prototyping and Production
One of the key advantages of CNC machining is its ability to support both rapid prototyping and large-scale production. During the prototyping phase, CNC machining enables quick iterations of part designs, allowing for precise testing of form, fit, and function. This ability to quickly produce high-accuracy prototypes is crucial for innovation and timely project development.
Once prototyping is complete, CNC machining seamlessly transitions into full-scale production, ensuring that each part is consistently produced to specification. This is particularly important for aerospace, where safety and performance depend on the highest level of precision and reliability.
Looking Ahead: Future Trends in Aerospace CNC Machining
As the aerospace industry continues to evolve, CNC machining is also adapting to new challenges and opportunities. Emerging technologies like artificial intelligence (AI), machine learning (ML), and robotics are shaping the future of manufacturing, driving greater automation and precision in machining processes. Hybrid manufacturing methods, which combine CNC machining with additive manufacturing, are also gaining traction, offering even greater flexibility in part design and production efficiency.
Furthermore, the aerospace sector is increasingly focused on sustainability, with manufacturers exploring new materials and designs that reduce fuel consumption and environmental impact. CNC machining will continue to play a critical role in bringing these innovations to life.
Conclusion
CNC machining is a critical tool in the aerospace industry, enabling the production of high-precision, complex parts that meet rigorous safety and performance standards. By understanding the processes, materials, and challenges associated with aerospace CNC machining, manufacturers can make informed decisions that ensure the creation of reliable, durable components. As the industry moves toward greater innovation and sustainability, CNC machining will remain at the forefront, helping shape the future of aerospace manufacturing.