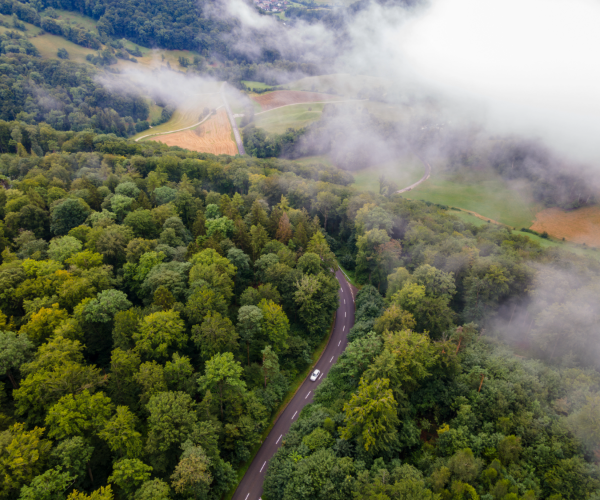
You may also like:
CNC Lathes: What’s on the Horizon?
Digital Twins: A New Era of Innovation
Vertical Turning Lathes: Precision and Power Redefined
In today’s evolving industrial landscape, manufacturers face the growing challenge of balancing productivity with environmental responsibility. Natural resource depletion, climate change, and the demand for eco-friendly practices have placed manufacturing—one of the largest contributors to carbon emissions—under increasing pressure to adapt. Sustainable machining is no longer a trend; it is a necessity.
What is Sustainable Manufacturing?
Sustainable manufacturing refers to the creation of products through processes that minimize negative environmental impacts, conserve energy and natural resources, and prioritize safety for workers and communities. Beyond environmental benefits, sustainable practices improve efficiency, reduce waste, and create economic and social value—helping manufacturers remain competitive in a shifting global market.
At the heart of sustainable manufacturing is green machining—an approach that reduces energy consumption, minimizes waste, and optimizes machining processes without sacrificing quality or performance.
The Role of Machining in Sustainability
Machining plays a crucial role in producing components used across countless industries. However, machining operations are energy-intensive and generate material waste, often requiring fluids and materials that impact the environment.
Sustainable machining focuses on:
Reducing energy consumption
Minimizing material waste and emissions
Optimizing cutting tool use and machining paths
Enhancing machine tool efficiency
Recycling metal chips and swarf
Implementing virtual simulations and digital twin technologies for process optimization
By addressing these factors, machining operations reduce their environmental footprint while improving cost-efficiency and productivity.
The Importance of Energy Efficiency in Machining
Energy use is a significant factor in machining sustainability. Studies reveal that non-cutting operations—such as spindle motors, coolant pumps, and fans—can consume over 30% of total machining energy. Implementing smart control systems, powering down idle equipment, and optimizing cutting parameters can significantly lower energy usage.
Designing machines and processes with energy efficiency in mind is critical to achieving both environmental and economic goals.
Building a Sustainable Future in Machining
Sustainable machining is an evolving journey that blends technology, strategy, and environmental responsibility. Key areas of focus include:
Energy-efficient machine tool design and operation
Support for dry machining and MQL techniques
Integration of digital tools for virtual simulation and optimization
Recycling of metal waste from machining operations
Continuous research toward reducing carbon impact
As industries move toward more sustainable operations, machining practices must evolve in parallel—delivering precision and performance while protecting resources and the environment.
Customization and Flexibility
With access to real-time insights, machining facilities can respond quickly to customer demands, offering greater customization and flexibility. Predictive analytics helps manufacturers anticipate market trends, allowing them to adapt production processes accordingly.
Shaping What Comes Next
Sustainability in machining isn’t just about reducing environmental impact—it’s a smart investment in efficiency, cost savings, and long-term success. By adopting energy-efficient technologies, optimizing material use, and embracing digital manufacturing, companies can enhance productivity while minimizing waste.
The future of machining lies in cleaner, smarter, and more efficient manufacturing. Every step toward sustainability strengthens the industry, ensuring a balance between high-performance production and responsible resource management.