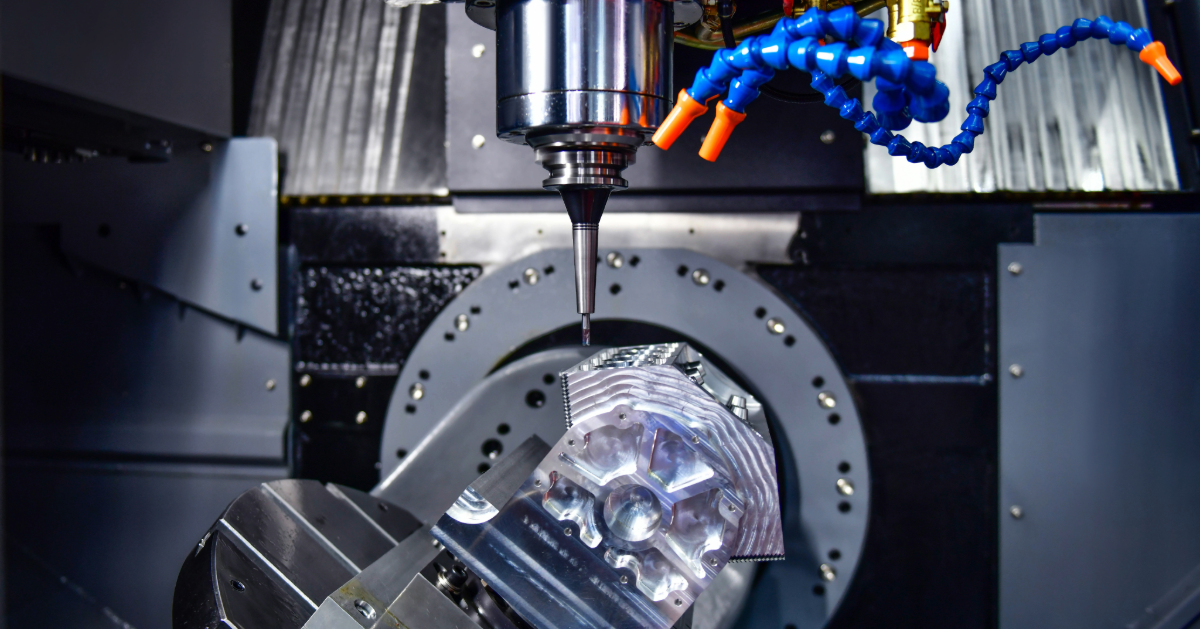
You may also like:
Two Spindle Machines: Boosting Productivity
Comparing 3-Axis to 21-Axis
CNC Lathes: What’s on the Horizon?
Tool selection directly impacts CNC machining quality, efficiency, and cost-effectiveness. From material choice to tool geometry and coatings, every factor plays a key role in achieving precision and long tool life. Here’s an overview of how to optimize tooling selection for your CNC operations.
Tool Materials: Choose Wisely for Durability and Performance
The material of your cutting tools determines their durability, heat resistance, and wear performance. High-quality, well-maintained tools are essential for maintaining machining accuracy over time.
- High-Speed Steel (HSS): Tough and versatile, HSS is cost-effective but less durable than carbide or ceramic.
- Carbide Tools: Carbide offers superior hardness and wear resistance, ideal for high-speed or hard material machining. Though more expensive, carbide tools last longer and improve cutting performance.
- Ceramic Tools: Extremely hard and heat-resistant, ceramic tools are perfect for high-speed machining of tough materials, offering great surface finishes and extended tool life.
For even better performance, PCD (Polycrystalline Diamond)-tipped tools provide exceptional durability and tool life—up to four times longer than carbide tools. Though PCD tools come at a premium, their ability to run faster and last longer can result in significant cost savings over time.
Coatings: Boost Tool Life and Performance
Coatings like Titanium Nitride (TiN), Titanium Carbonitride (TiCN), and Diamond-Like Carbon (DLC) enhance tool durability and reduce friction.
- TiN Coating: Increases hardness and heat resistance, suitable for general applications.
- TiCN Coating: Offers higher wear resistance and is ideal for abrasive materials.
- DLC Coating: Reduces friction and improves wear resistance, perfect for high-speed machining.
These coatings help tools last longer, maintain precision, and provide smoother finishes.
Tool Geometry: Optimize for Performance
Proper tool geometry is crucial for achieving the best results in chip evacuation and surface finish. Geometries with positive rake angles and higher helix angles allow better chip flow, reducing cutting forces and tool wear. For smooth surfaces, tools with smaller rake angles and adequate clearance angles minimize built-up edges and improve finishes.
Material, Complexity, and Tolerance: Tailor Your Tool Selection
The type of material, complexity of the machining process, and required tolerance levels all influence tooling selection. Harder materials like stainless steel require tools with advanced coatings or materials, such as carbide or PCD, to handle tough cutting conditions.
- Material: Harder materials need more durable tools.
- Complexity: Intricate designs may require specialized geometries for precision.
- Tolerance Levels: Tight tolerances demand tools with minimal deflection and vibration.
Cost Considerations: Focus on Total Cost of Ownership
When selecting tools, focus on the total cost per linear foot machined, not just the initial price. Higher upfront costs for tools like PCD can be offset by their longer lifespan, faster speeds, and fewer tool changes. Brazed carbide inserts offer a more economical option, providing up to 75% cost savings compared to solid carbide tools without sacrificing performance.
Optimizing Tool Life
To maximize tool life, ensure tools are used within their design parameters, and monitor tool wear regularly. Factors like chip load and cutting speed directly affect tool lifespan. A well-maintained tool will offer optimal performance, reduce production downtime, and extend machining efficiency.
Conclusion
Tooling selection for CNC machines is essential for achieving high-quality, cost-effective results. By considering factors like material properties, coatings, geometry, and tool life, manufacturers can optimize their machining processes. Whether you’re using carbide, PCD, or carbide inserts, making informed tool choices will lead to greater precision, improved efficiency, and lower overall costs.